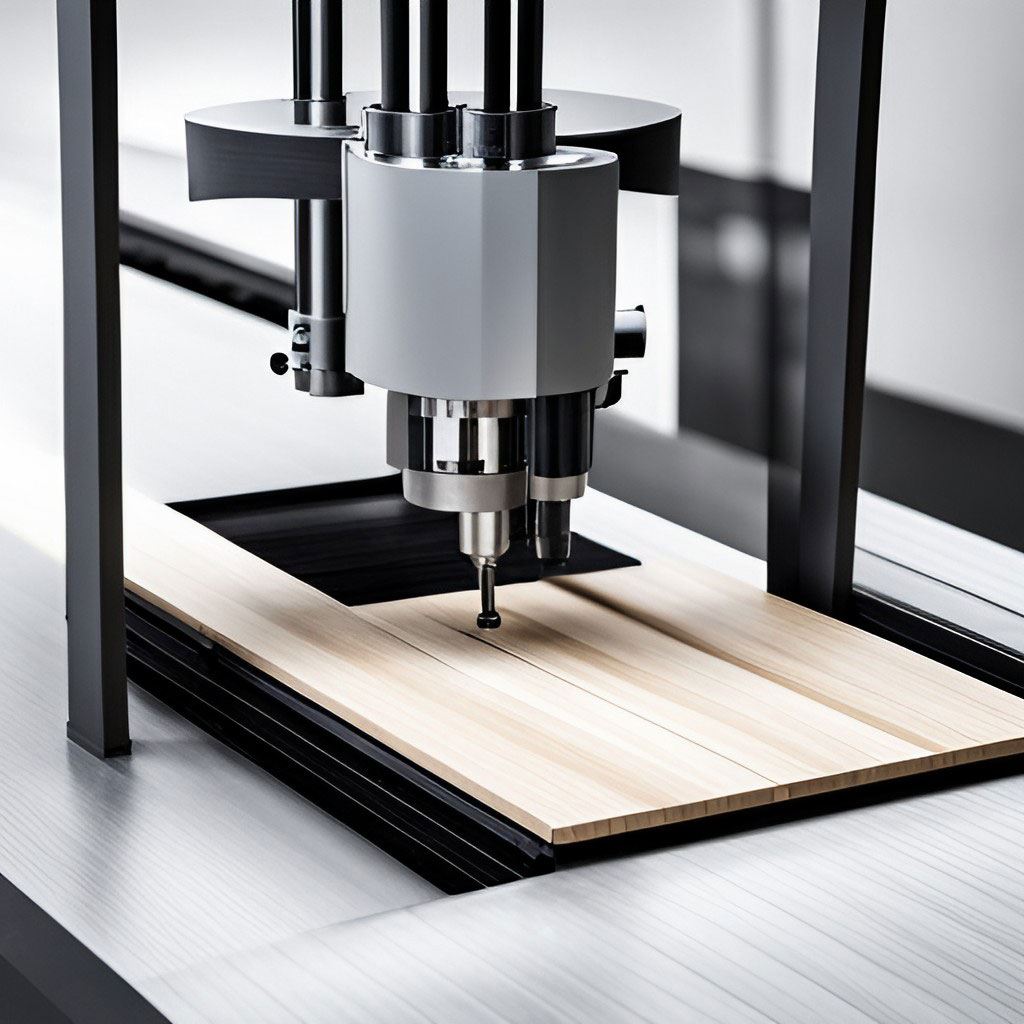
When preparing design files for production on a Zünd CNC router, it's a common practice to use different colors to represent various tools or actions. This color-coding system helps in quickly identifying the type of operation required for specific parts of the design, such as cutting, scoring, engraving, or routing. Below is a suggested list of color naming conventions that can be used for calling out different tools or actions on the Zünd CNC router. It's important to note that these are suggestions, and actual preferences might vary based on the specific workflow or settings of your Zünd equipment and its accompanying software.
Suggested Color Naming Conventions for Zünd Tools
- Red: Cut Path – For full cuts through the material.
- Blue: Score Path – For creases or folds, not cutting all the way through the material.
- Green: Kiss Cut – Slightly cuts the top layer of material without cutting through the entire thickness, commonly used for stickers or labels.
- Yellow: Perforate Path – For creating a perforated line, allowing the material to be easily separated or torn.
- Orange: Engraving Tool – Used to mark or engrave the surface of the material without cutting through it.
- Purple: Routing Path – For deep engraving or creating pockets in the material.
- Black: Marking Path – For non-cutting operations that require marking the material, possibly with pens or markers.
- Cyan: V-Cut – Specifically for making angled cuts that facilitate folding, commonly used in packaging designs.
- Magenta: Half Cut – For cutting halfway through the material, often used for creating foldable tabs or easy-tear sections.
Best Practices for Implementing Color Conventions
- Consistency: Once you decide on a color scheme, maintain consistency across all your design files. This helps machine operators quickly understand your designs without needing to reference a key each time.
- Documentation: Create a clear guide or legend that explains your color-coding system. This document should be accessible to everyone involved in the production process.
- Software Compatibility: Ensure that the colors you choose are distinctly recognizable and compatible with the Zünd cutter’s software. The software should be able to accurately interpret each color according to the intended tool or action.
- Communication: Discuss your color-coding scheme with the team or individuals operating the Zünd CNC router. This ensures that everyone is on the same page and understands the significance of each color.
- Test Cuts: Perform test runs on scrap material to ensure that the color assignments correctly correspond to the intended tools and actions. Adjust as necessary based on the results and feedback from the machine operators.
Implementing a color-coding system for tool and action designation in your design files can significantly streamline the production process on a Zünd CNC router. By clearly communicating the intended operations through color, you can reduce setup times, minimize errors, and enhance overall efficiency.
Adopting a consistent naming and color-coding convention for various operations like draw, score, crease, and others when using a Zünd CNC router can significantly streamline the production process. Here's a tailored approach to naming and possibly assigning colors for each operation, taking into account your specific terms and including "CutContour" for thru-cut operations:
Custom Naming and Color Assignments
-
Draw
- Color: Blue
- Description: Used for operations that involve drawing or plotting with a pen tool on the material.
-
Score
- Color: Orange
- Description: For creating a shallow cut that facilitates folding or bending without cutting through the material.
-
Crease
- Color: Yellow
- Description: Similar to scoring but specifically designed for creating more defined fold lines, often in thicker materials.
-
Kiss-cut
- Color: Green
- Description: A light cut that only goes through the top layer of the material, commonly used for sticker sheets.
-
Punch
- Color: Red
- Description: For creating small holes or cutouts in the material, akin to punching.
-
Drill
- Color: Cyan
- Description: Used for operations that require drilling holes through the material.
-
Engrave
- Color: Purple
- Description: For engraving designs or text into the surface of the material without cutting through it.
-
V-cut
- Color: Magenta
- Description: Designed for making a V-shaped cut, typically used for creating angled folds or joins in materials.
-
Bevel-cut
- Color: Dark Green
- Description: A cut made at an angle other than 90 degrees to the surface of the material, used for creating beveled edges.
-
Thru-cut (CutContour)
- Color: Black
- Description: A complete cut through the material, following the outer contour of the design. This term is specifically associated with the color or naming convention "CutContour."
-
Route
- Color: Grey
- Description: For hollowing out areas within the material or creating complex 3D shapes.
Implementing the Convention
- When setting up your design files, each operation should be assigned its designated color, which will correspond to specific tools or blades on the Zünd router. This ensures that the machine accurately executes the intended action on each part of the design.
- It's crucial to coordinate with your production team and make sure everyone is familiar with these conventions. This familiarity prevents mistakes and accelerates the setup process.
- Maintain a reference chart or guide accessible to all operators and designers that outlines these colors and their corresponding actions. This can be especially helpful for new staff or when troubleshooting production issues.
By standardizing the naming and color-coding of operations in your design files, you ensure clarity and efficiency in your Zünd CNC routing processes. This method not only streamlines communication among team members but also minimizes errors, resulting in a smoother, more predictable production workflow.